Computational fluid dynamics (CFD) is a very important tool for most of the fields of engineering. From simulating airflow around a car to optimising the cooling system in your smartphone, CFD has the great capability of analysing and predicting fluid behavior. In this article, we will explore the mysteries of CFD, exploring its applications, limitations, and how it shapes the future of engineering and innovation.
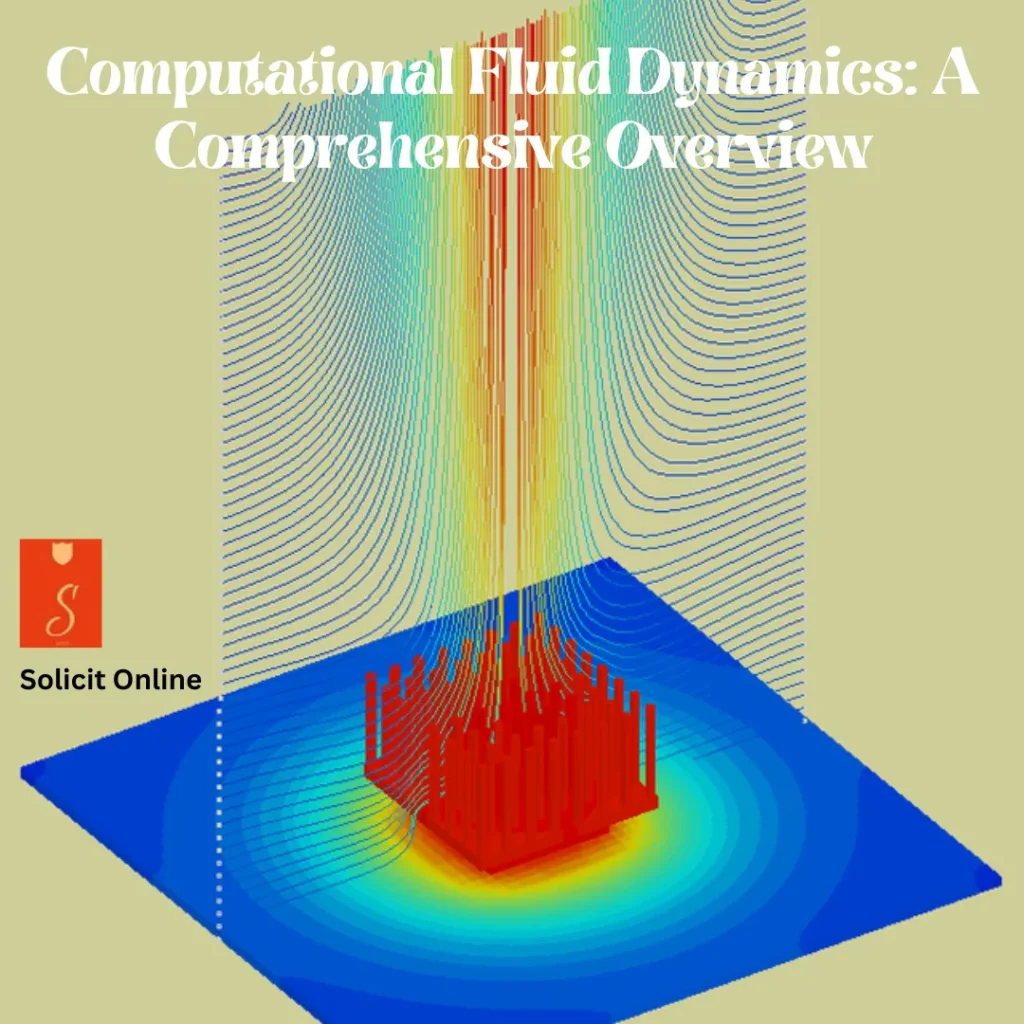
What is CFD?
CFD is the numerical solution-based study of fluid flows. CFD may be used to solve complicated issues involving fluid-fluid, fluid-solid, or fluid-gas interactions. Aerodynamics, hydrodynamics, and biological performance of medical devices are the main engineering domains where CFD studies are generally used to determine the concerned variables and capture flow characteristics. Physical rules in the form of partial differential equations are engaged in fluid dynamics. Sophisticated CFD solvers convert these rules into algebraic equations and can numerically solve these equations. The designers concentrate on using CFD to enhance design and performance. This is normally accomplished via a difficult trial and error procedure. Based on their judgement and expertise, the designer uses CFD findings and applications to improve designs. Further, CFD simulations have to be merged with an optimization method, which is dependent on an automated iterative process for design improvement, in order for a technique to be considered an optimization technique.
Why do we need CFD?
CFD studies have a significant potential to cut down on the amount of time spent on the design process, and as a result, they are both more affordable and more expedient than traditional testing for the purpose of collecting data. In addition, while doing tests in real life, only a select few of the required values can be evaluated at one time. But when doing a CFD study, all of the quantities can be measured at the same time with high accuracy in both space and time.
It is important to keep in mind that the numerical simulation method makes several assumptions, approximations, and refinements. As a result, these values must be determined by tests and/or CFD simulations. Validation and verification of CFD results are therefore required.
How is CFD implemented?
Iterative methods are used to solve the equations used in CFD. Convergence is very critical for outcomes that are based on residuals. Varied studies have different ways of evaluating convergence criteria, but the strategy that is most often used is to monitor residuals and look for certain patterns, such as when they fall below a threshold or become static. The degree to which various flow variables are weighted in significance influences the convergence criterion. These computer methods make use of certain techniques for the formation of grids, the solution of problems, and the approximation of systems. Therefore, the use of the appropriate computational methodologies is very necessary for the CFD study. An analysis using CFD will often be broken down into the following three stages:
Pre-processing
In CFD simulation, the first stage is called pre-processing, and if it’s done correctly, it may contribute to the definition of the required parameters in an accurate manner. Depending on the complexity of the design, the geometries are created either using computer-aided design (CAD) software or in the CFD environment. If the geometry was made using CAD software, the it is need to be imported into the CFD environment using a file format that is compatible with that environment.
During this step, you will be tasked with determining the computational domain and subdividing it into a number of smaller parts that is called grid generation or meshing. The pre-processing steps include model creation, meshing it, specifying the characteristics of the materials that are to be modelled, and establishing the boundary conditions and constraints.
As was noted before, the quality of a CFD analysis is only as good as its executor; specifically, how accurately the model can be set up by the designer. This is because the initial design will ultimately have an effect on the model in the subsequent stages of analysis. So, precise modelling is very necessary for evaluating the accurate performance characteristics of the problem.
Solver
The solver is the component that is responsible for doing the actual calculations, and during the solution phase, processing capacity is needed. There is more than one solver accessible, each of which has a unique level of effectiveness and competence when it comes to addressing specific phenomena.
Post-Processing
In the last step, which is called “post processing,” the data that were gathered are examined and displayed. At this point, the analyst has the ability to check the data, and based on the results that were acquired, conclusions may be reached. The findings may be presented in a variety of formats, such as images or animations, graphs, or tables, for instance.
Application Areas of CFD
A CFD analysis is used extensively in a variety of industries, including the automotive, mechanical, process and chemical, energy sector, pollution dispersion, climate modelling, biological, and aerospace sectors. CFD analysis is employed in industries whenever they conduct research and innovation on new products before their actual fabrication. Various employment possibilities are made available for research and development of new products or for improving the performance of products already available in the market, and these things require hard work, skills, and areas of expertise. The complex analysis requires more computation than the simple one. However, CFD simulation costs have decreased significantly in recent years as a result of improvements in processing capacity and the advancement of CFD software. This offers accessibility to all kinds of companies to take advantage of the CFD tool.
Verification of CFD
Verification is an important task in CFD analysis. The verification ensures the implementation process of the CFD tool as well as the algorithm. This testing is done by comparing the known solution or analytically calculated data to ensure its accuracy and realability. So it is a necessary step for the correct analysis of the chosen problem.
Validation of CFD
The validation is different from the verification, but it is also equally important in CFD analysis. The validation process compares the CFD simulation results with experimental data or empirical data to access the CFD model capability to accurately predict the real-world problem and predict the behavior. It ensures the computational model’s suitability for a particular application if the simulation results close to an acceptable error of margin with experimental data.
Challenges and Limitations
Over the past decade, Computational Fluid Dynamics (CFD) has made significant strides, revolutionizing engineering analysis and design. However, despite these advancements, several obstacles and constraints persist, impacting the accuracy, reliability, and practicality of CFD models. Challenges include tackling the complexity of real-world phenomena, refining turbulence modeling techniques, achieving high-quality mesh generation while preserving computational efficiency, managing computational costs, and navigating resource limitations. Balancing computational expenses with simulation precision remains a formidable task, particularly for extensive simulations or parametric studies.
Future Trends and Innovations
The integration of artificial intelligence (AI) for more intelligent forecasts and the use of high-performance computing (HPC) for the effective management of large-scale simulations are driving significant breakthroughs in CFD. In order to improve the accuracy of CFD forecasts, researchers are highlighting the significance of uncertainty quantification and verification/validation procedures. The advancement of user-friendly software and interdisciplinary collaboration are making CFD increasingly accessible and industry-relevant. This is especially true when it comes to advancing environmental conservation and sustainability. Understanding the evolving field of CFD research requires constant learning and adaptation, which presents great opportunities for solving real-world problems and influencing a more environmentally friendly future.